introduction
Easy opening is a cover for metal cans in the food canning industry. Although there are many procedures for the easy-opening products, they generally include: sheet metal → basic lid forming → pull ring assembly → post-processing → imaging visual inspection → lid packing. There are two types of easy-open covers: circular and non-circular. Easy-open cover refers to non-circular open covers, such as elliptical, square, and horseshoe shapes.
The easy-open lid is used for the lid and opening of cans. As its name implies, it should be easy to open when it is eaten. Therefore, when the lid is processed, the lid surface is pre-inscribed with a certain depth of nicks, and a pull ring is riveted. The lid can be completely pulled along the nicks. For reasons of canned food safety, the lids are required to not be rusted or corroded after the foods are packaged in cans until the food is consumed. Therefore, tinplate materials used for easy opening of lids are generally subjected to a coating process in advance. A layer of corrosion-resistant paint is applied to the surface of the tinplate material so that the lid will not rust or corrode during the process of packaging the food. However, the processing of the score line will undoubtedly destroy the coating on the lid, so the cap must be applied after the score line. In order to open the can with the largest opening, the track of the general score line is similar to that of the cover body, and is the equidistance line of the cover body inward track, so the circular easy-open cover score line is round and shaped. The trajectory of the easy-opening score line is also its similar shape.
Starting from the traditional scratch line coating technology and process method introduction, the existing limitations and deficiencies were analyzed. For the improvement of the supplementary coating process and equipment optimization, the application principle of the new numerical control special-shaped easy-open cover cutting line coating technology was introduced. Good use performance.
1 Traditional grout coating technology
The materials used for recoating are generally phenolic resin coatings, epoxy-phenolic resin coatings, acrylic resin coatings, and aluminum pastes. These types of coatings have corrosion resistance, good adhesion, flexibility, non-toxicity, and tastelessness. , In line with food hygiene and safety requirements, in addition, for the storage, transportation of paint containers, pipelines, also require high corrosion resistance, and easy to disassemble, easy to clean.
Due to the characteristics of the coating used for scratch coating and the cross-sectional shape of the reticle, the cross-sectional shape of the sprayed paint is generally fan-shaped rather than cylindrical, ie, it has directionality, so it is easy to open the circle. The capping process is generally irreversible, the cap rotates, so that the sprayed coating on the cap looks like a circle with a more uniform ring, and is also more beautiful.
For irregularly shaped easy-open covers, due to the irregularities of the scribe lines, the reticle coating process is relatively complicated. The completion of the conventional special-shaped easy-open cover reticle coating process mainly includes the following methods:
Manual brushing The paint is applied directly by the worker on the surface of the cover. This kind of recoating method has a simple process, high labor intensity, low work efficiency and unfavorable uniformity of the coating layer, and is only applicable to a cap type in which the lot size is particularly small and the input-output ratio is not high or is not commonly used.
Pure mechanical method to complete the special coating of the easy-open cover with the special shape must have the following steps: capping → capping → cap feeding → cap positioning → cap capping → cap rotation (cap does not rotate) → spray gun translation (following ) Make up → cover down → cover away. In addition to the manual completion of capping, each of the remaining steps must be automatically implemented using conventional mechanical equipment. The actions between each step must be coordinated with each other, cooperate with each other, have good synchronization, and cannot have a chain of action. Can't have a move ahead. Purely mechanical way to complete the special coating process of easy-open cover, the machine structure is very complex, the power transmission in a three-dimensional space criss-cross, there are many steps to use the eccentric wheel, cam to complete, such as intermittent capping, intermittent delivery cover to use X Axial eccentrics are used to achieve the top and cover down the use of the Y axis of the lifting cam to achieve, and complete spray gun translation (following) action is a double cam molding mechanism. Eccentric wheels and lifting cams are easy to design and process according to the cap feeding step and lifting stroke. For different cap types and different models, as long as the cap feeding step and the lifting stroke are designed to be the same, the eccentric cam and the lifting cam can be used universally. The double-layer molding cam that completes the translational motion of the spray gun is designed according to the trajectory of the engraved line in the cover type. Different cap-shaped forming cams are not the same, and the machining accuracy of the forming cam is also relatively high because the forming cam is slightly processed. Deviation, the trajectory is not the same, the paint sprayed by the spray gun is not necessarily made up on the engraved line, the product quality of the corresponding lid can not meet the requirements, debugging and installation is very troublesome, easy to open the cover The cover type non-standard, a cover type of product demand is relatively not very large, and the structure is so complex, if the machine output is not high, the production efficiency is very low, if the different cover type share one, then change Replacement of cap-type spare parts (shaping cams) is required when capping, and replacement of cap-type spare parts is particularly troublesome, and product replacement is difficult, and with the use of time, mechanical wear will affect the same Precision, post-maintenance costs high, so profiled purely mechanical way of easy open up more suitable for larger production coater, do not change the type of shaped easy open lid production.
The combination of mechanical method and numerical control technology completes the various steps of the special-shaped easy-opening cover coating process by combining the mechanical mode with the numerical control technology, that is, mechanically completing the actions of capping, capping, cap feeding, cap positioning, capping, and the like. The numerical control system and servo drive technology are used to replace the power transmission actuators and cam transmission processes that complete the transformation of the original complex gears and transmission shafts. The electronic cams are used instead of the traditional mechanical cams to replace the various actuator units with servo motor direct drive mechanisms. , Speed ​​synchronization control and position control, to achieve three-dimensional trajectory automatic coating, that is (X-axis and Y-axis synthesis of the joint) and the gun (Z-axis) up and down movement.
At present, the control method using numerical control technology is rarely used in the production equipment of the domestic easy open cover industry. The following will introduce in detail the numerical control technology of this profiled easy-opening capping line coating process.
2 Application of Numerical Control Techniques for Irregularly Opening and Covering Marking Lines
2.1 Project Design
With the combination of mechanical and numerical control technology to complete the cover coating process of special shape and easy opening, the mechanical method only needs to complete the capping → capping → cap feeding → cover positioning → capping and other actions, capping is still done manually, and A series of actions such as cap → cap feeding → cap positioning → cap feeding and the like can be completed simply by an eccentric or an intermittent indexer, the mechanical design is very simple, and the trajectory compensation (including the X-axis and Y-axis) is completed. Motion synthesis, spray gun up and down movements and other complex actions) are all done by the CNC system.
Take the shaped cover T501 as an example. The specific dimensions are shown in Figure 1. The process requirements are as follows:
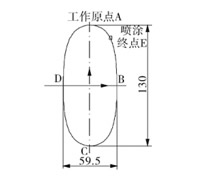
Figure 1 T501 oval cover size
The X axis is the horizontal axis. The servo motor directly drives the ball screw to drive the gun to move left and right. The length of the X axis motion area is 100mm.
The Y axis is the vertical axis. The servo motor is used to directly drive the ball screw to drive the gun forward and backward. The length of the Y axis motion area is 300 mm.
The Z axis is the vertical lifting axis. When the positioning is completed, the Z axis moves down to near the top of the cover nick. The solenoid valve of the spray gun is started and the injection jet action is started. After the XY axis trajectory linkage is completed, the injection jetting operation is ended, rising. To the original zero position, the Z-axis servo can be single action, and the length of the motion area is 100mm.
Point A is the working origin of the servo system. The X, Y axis's trajectory is A-B-C-D-A-E-A. The spray gun uses an electron gun and the working range is A-B-C-D-A-E. After the spraying finishes, the Z-axis picks up and the X, Y, and Z axes quickly return to the working origin A, waiting for the start trigger of the next cover positioning signal, and so on.
The process control process is shown in Figure 2:
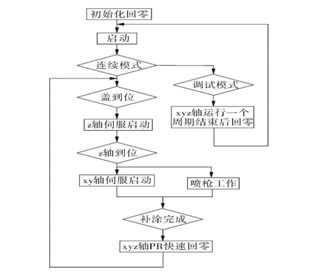
Figure 2 coating process control process
2.2 Selection of CNC System
The CNC system uses Delta's PUTNC-H6C, its main features: Open system architecture, maximum response speed 500KPPS encoder feedback, to meet the needs of rapid positioning, in addition to linear interpolation and other motion control, but also to display the screen , parameter setting, program editing, PLC logic control, etc., can be applied to all kinds of industrial machinery and automation equipment [3].
AC servo drive uses Delta-A series driver ASD-AB, with position P-CURVE and speed S-CURVE smoothing function, can smooth the movement command, make the motor produce continuous speed and acceleration, can be improved The characteristics of motor acceleration and deceleration are also smoother and smoother in the operation of the mechanical structure.
The pitch of the X-axis/Y-axis slide screw is 5mm, and the X-axis/Y-axis servo encoder resolution is set to 100000ppu by the electronic gear ratio function. X-axis servo and Y-axis servos require two-axis interpolation function, because the speed is fast, the stroke is short (for example, the circumference of the trajectory line of T501 oval cover is 300mm, in which the long axis is 130mm, the minor axis is 65mm), and the moment of inertia is large. The response time requirements are fast, so the servo drive mechanism uses the coupling directly, adjusting the response time of the servo as fast as possible and adjusting the tuning time. The servo system's high precision, stability, responsiveness, and self-adaptive ability to load changes are fully utilized. The linkage characteristics of the drive system are optimized, and the entire drive system achieves ideal mechanical performance.
The basic configuration diagram is shown in Figure 3 [4]:
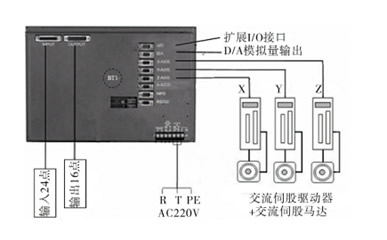
Fig. 3 Basic configuration of numerical control system
The controller memory has 512K memory space, the basic G code programming, with the standard CNC keyboard or CAD/CAM, can be input via USB or computer RS232C interface, because it is a CNC system, when the trajectory changes, just prior to the different cover The control program of the model and its operating parameters is stored in the control system. A cover type selector switch (see Figure 4) is set on the panel of the LED panel. After the control system is selected, the corresponding control program will be called and the production process will be carried out according to the selected program. The replacement of the machine cover type is very convenient, and the production efficiency of the machine is greatly improved.
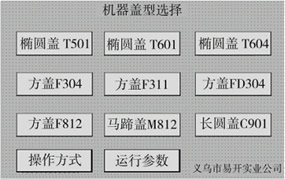
Figure 4 LED panel
Due to the high precision of the control, the CNC control method is characterized by high acceleration, smoothness, and fast response. The trajectory of the cover applied by the machine is beautiful, the coating film is uniform, and the repeat accuracy is high. Since the device reduces the number of transmission mechanisms, the noise is very small. Easy to change, because HC6 has the ability to drive six servo axes, it can also be designed into a one-two-to-two way to control the production of two different shaped cover types. This kind of flexible control method not only improves the production efficiency of the equipment. , And the investment is not, is a cost-effective multi-axis servo synchronous control program.
CNC system can refer to the actual needs of production and each person's preferences choose different configurations, such as industrial computer, HMI + PLC + motion control module and so on. The numerical control of manufacturing equipment is the development direction of special equipment manufacturing.
2.3 The characteristics and advantages of the application of numerical control system technology (see Table 1)
Table 1 Comparison of main technical parameters and advantages and disadvantages of the two processes
Compare items
Traditional reticle coating method
Numerical control method
Equipment processing cycle
Long (requires high precision, complex and difficult installation of machine tools)
Short (simple installation)
Production beat
SLOW
fast
Change type
Difficult, time-consuming
very convenient
positioning accuracy
Low (wear after prolonged use, reduced accuracy)
High (less than 2mm)
Response time
SLOW
Fast (can increase speed according to cover type)
Coating pass rate
low
high
Average time between failures
On average, there is a 1-hour failure time every 11 hours
Low (few failures)
Number of operating workers
2 machines 4 people
2 machines 2 people
Maximum power consumption
2.2kW
1.5kW
noise
High (Power transmission, mechanical cooperation with large noise)
Low (single cover and lid transmission only, lower)
Extensibility
Can't
Can be extended (one for two, one for three, etc.)
Value for money
low
high
3 Conclusion
Through the application of numerical control system, the traditional mechanical cam connection is abandoned in the mechanical structure, replaced by a high-precision servo system, and the position and speed of the horizontal X axis and the vertical Y axis are synchronously controlled by a precision screw, respectively. The original mechanism of the complex transmission of the cam, this control system is stable, easy to operate, easy to change, high movement accuracy, mechanical wear, simple maintenance, scalability, and the CNC system has been gradually processed from the original simple parts and components Applied to automated manufacturing equipment.
Excerpt from: Packaging and Food Machinery, 2011-04
Green Silicon,Silicon Carbide Grit ,Silicon Carbide Powder ,Silicone Carbide
Petroleum & Products Co., Ltd. , http://www.nbhardcoke.com