The problem of shrinkage of
plastic parts is mainly reflected in the surface shrinkage and internal shrinkage. Both of these shrinkages are caused by insufficient filling of the melt when the thicker part is cooled. We often encounter situations where the pressure is increased, the water inlet is increased, the injection time is prolonged, and the shrinkage problem cannot be solved.
Among the commonly used raw materials, the shrinkage of the PC material is the most difficult to solve due to the fast cooling rate, and the shrinkage and shrinkage of the PP material is also difficult to handle.
Therefore, when encountering a serious shrinkage problem with thick parts, it is necessary to take some unconventional injection molding techniques, otherwise it will be difficult to solve the problem.
First of all, under the premise of ensuring that the injection molded parts are not deformed, the method of minimizing the cooling time is adopted to allow the injection molded parts to be prematurely released at a high temperature. At this time, the temperature of the outer layer of the injection molded part is still high, and the skin is not too hardened, so the temperature difference between the inside and the outside is relatively small, which is advantageous for the overall shrinkage, thereby reducing the concentrated shrinkage inside the injection molded part.
Since the overall shrinkage of the injection molded part is constant, the more the overall shrinkage is, the smaller the concentrated shrinkage is, and the degree of internal shrinkage and surface shrinkage is thus reduced.
The problem of shrinkage and concavation is caused by the temperature rise of the mold surface and the cooling capacity. The surface of the newly-formed injection molded part is still soft. The internal shrinkage hole that has not been completely eliminated forms a vacuum, which causes the surface of the injection molded part to be pressed under atmospheric pressure. Internal compression, coupled with the effect of shrinkage force, the shrinkage problem arises. Moreover, the slower the surface hardening speed, the more likely it is to cause dents, such as PP material, and the more easily the shrinkage holes are produced.
Therefore, after the injection molded part is prematurely released, it is appropriately cooled to maintain a certain hardness on the surface of the injection molded part, so that it is less likely to cause shrinkage. However, if the problem of shrinkage is serious, moderate cooling will not be eliminated. It is necessary to adopt a method of freezing water to make the surface of the molded part harden quickly to prevent shrinkage, but internal shrinkage holes will still exist. For materials with a soft surface such as PP, due to the effect of vacuum and shrinkage force, the injection molded parts may have the possibility of shrinkage, but the degree of shrinkage has been greatly reduced.
At the same time as taking the above measures, if the method of extending the glue injection time is used instead of the cooling time, the surface shrinkage and even the internal shrinkage cavity improvement will be better.
When solving the shrinkage hole problem, the mold cavity temperature is too low, which will increase the degree of shrinkage. Therefore, the mold is preferably cooled by machine water. Do not use frozen water. If necessary, increase the mold temperature, for example, when molding PC material. When the temperature rises to 100 degrees, the improvement effect of the shrinkage hole will be better. However, if it is to solve the problem of shrinkage, the mold temperature can not be raised, but it needs to be reduced.
Finally, sometimes the above methods may not completely solve the problem, but there has been an improvement in efficiency. If the problem of surface shrinkage must be completely solved, it is a last resort to have a proper amount of anti-shrinkage agent. Of course, transparent parts can't do this.
If the surface of the thick-walled part still has a sink mark, or if a plastic part such as a partial wall is encountered, the introduction of gas-assisted injection molding will be solved.
Gas-assisted injection molding is a novel plastic molding technology that introduces high-pressure gas into the thick-walled part of the part, creates a hollow section inside the injection molded part, completes the filling process, achieves gas holding pressure, and eliminates product shrinkage. The traditional injection molding process cannot combine the thick wall and the thin wall together, and the residual stress of the workpiece is large, it is easy to warp and deform, and there is a shrinkage on the surface.
The newly developed gas-assisted technology successfully produced thick-walled and siding products by hollowing out the thick-walled interior, and the surface appearance of the product was excellent and the internal stress was low. Lightweight and strong.
TV sets, home appliances, automobiles, furniture, daily necessities, toys, etc. have opened up new fields of application for plastic molding. Gas-assisted injection molding technology is particularly suitable for pipe-like products, thick-walled, partial walls (pieces of different thickness sections) and Large flat structural parts. Gas assist devices: including nitrogen generation and boosting systems, pressure control units and intake components. The gas-assisted process can be fully integrated with the traditional injection molding process (injection molding machine).
Reduce product weight (saving material) can be 40% higher, shorten molding cycle (saving time) up to 30%, eliminate sink marks, improve yield; reduce injection pressure up to 60%, can produce large parts with small tonnage injection molding machine, reduce operation Cost; extended die life, reduced manufacturing costs, and more stable structures such as thick roots, thick ribs, and connecting plates, increasing mold design freedom.
We are one of the leading Manufactures, Suppliers and Exporter of high quality Carbon Steel Flange in China.
Blind Flange as one of the carbon steel Forged Flange . Carbon Steel Blind Flange in different size, pressure and standard, could divided into some products, such as the Class 150 Blind Flange, Jis 10k Blind Flange , Blind Flange Price , carbon steel blind flange, En 1092-1 Blind Flange, Ansi b16.5 Blind Flange. And also could be done as the customer's drawing.
Product Description
class 150 blind flange, jis 10k blind flange, blind flange price, carbon steel blind flange, en 1092-1 blind flange, ansi b16.5 blind flange
Size
1/2"-120" (DN15-DN3000)
Pressure: Class150-Class2500
Standard
ASME, ANSI B 16.5/16.47,
JIS B2220
DIN 2527
EN1092-1 TYPE 05
GOST 12821-80
Material
ASTM A105. CS/SA 105/SA105N; CS RST37.2, S235JR; Q235; CS CT20; CS SS400, SF440; S235JRG2,P245GH,P250GH, P280GHM 16MN, 20MN ,20#
Coating
Black, Yellow paint; rust-proof oil; Antirust oil, Clear lacquer, Black lacquer, Yellow lacquer, Hot-dipped Galvanized, Electrical galvanized
Certificate
ISO9001:2008,
Capacity
30000tons/year
Main Market
Turkey, Italy, France, Spain, South Africa, Moroco, Dubai, Iran, Syria, Singapore, Vietnam, Austria, USA, Canada, Mexico, Korea, Thailand, India, Bulgaria, Russia and so on
Delivery time
30days after receipt of advanced payment or original LC ,Common size large quantity in stock
Payment term
T/T, L/C
Inspection
Factory In-House Check or The Third Party Inspection
Packaging
Plywood Pallets/ Wooden Case Or As Per customer's request
MOQ
No Limit
Technics
Pressed
Origin
China
Sample
Sample can be free, but customer have to pay transport cost
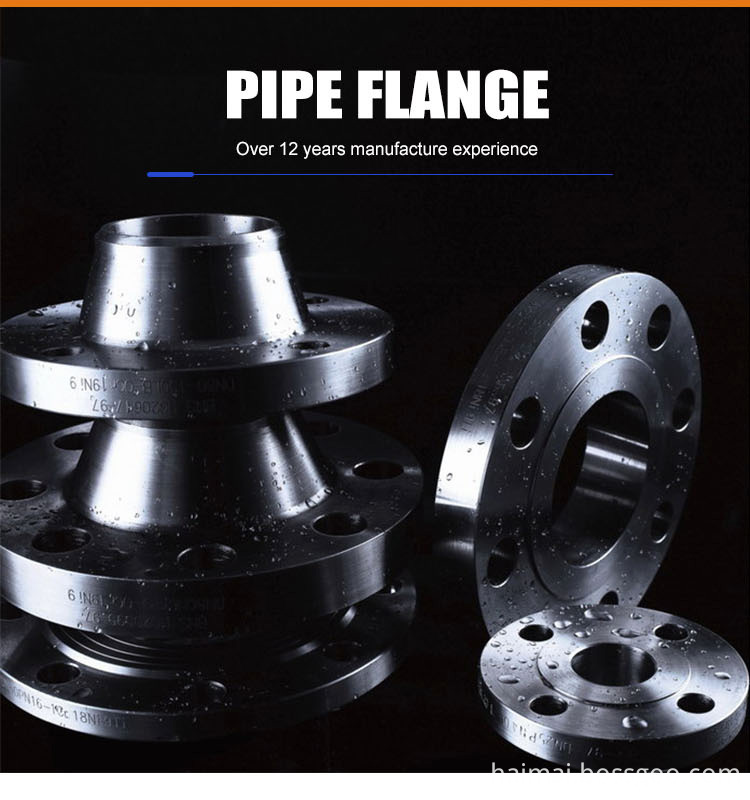
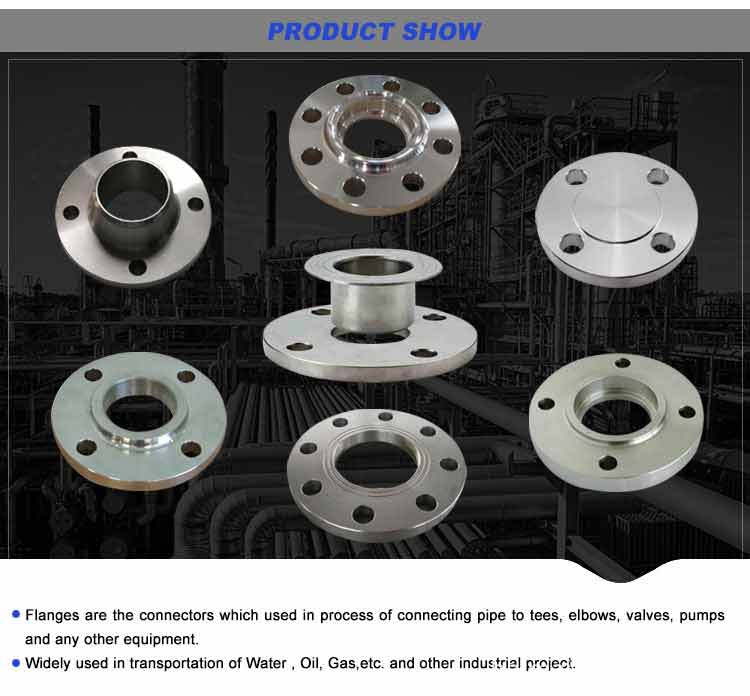
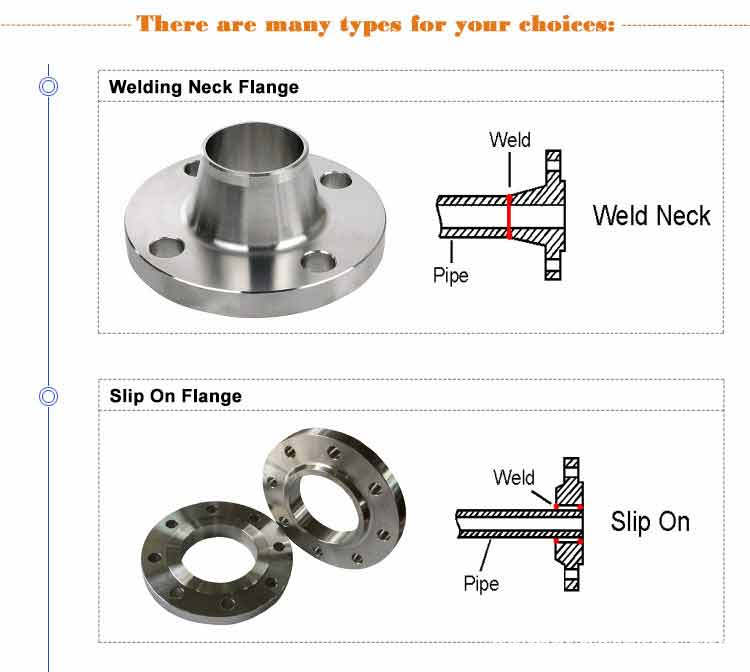
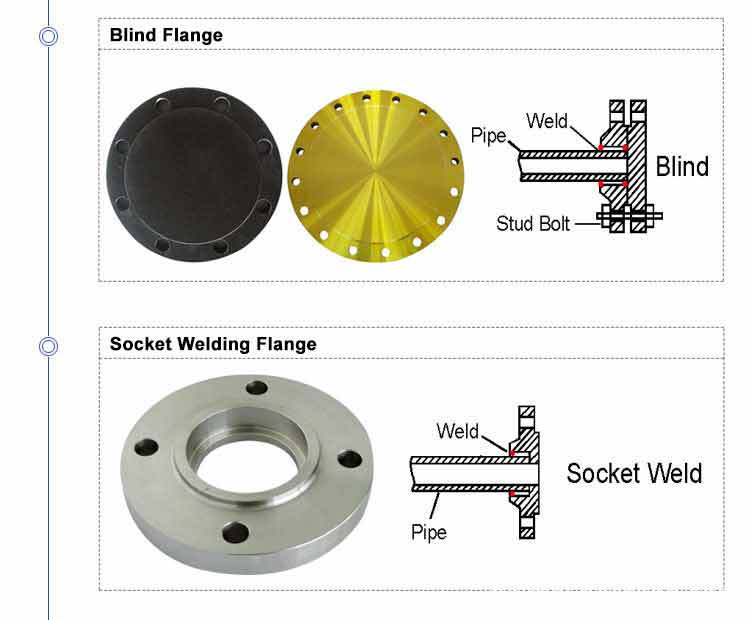
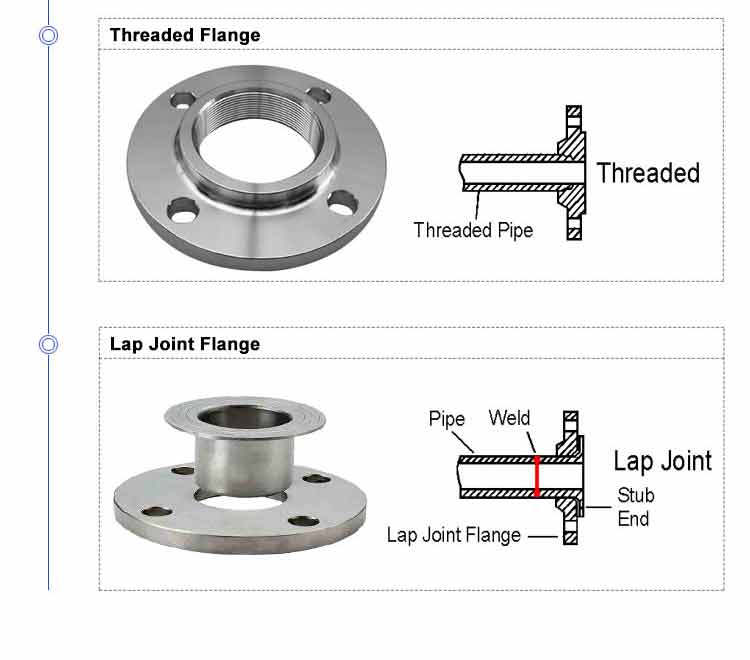
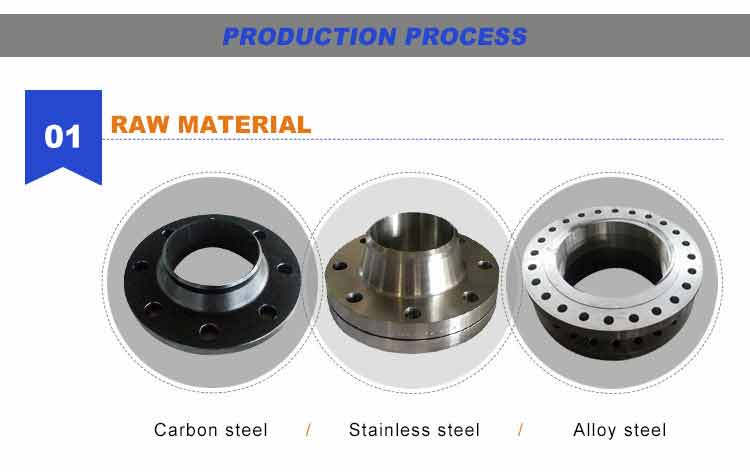
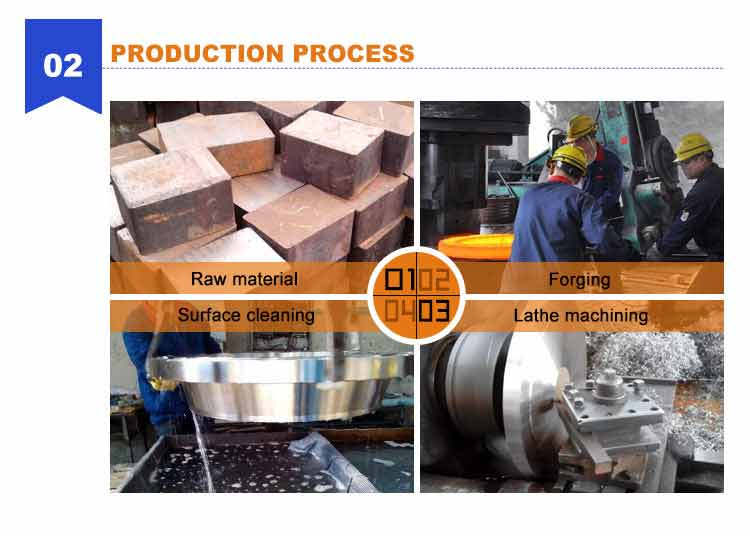
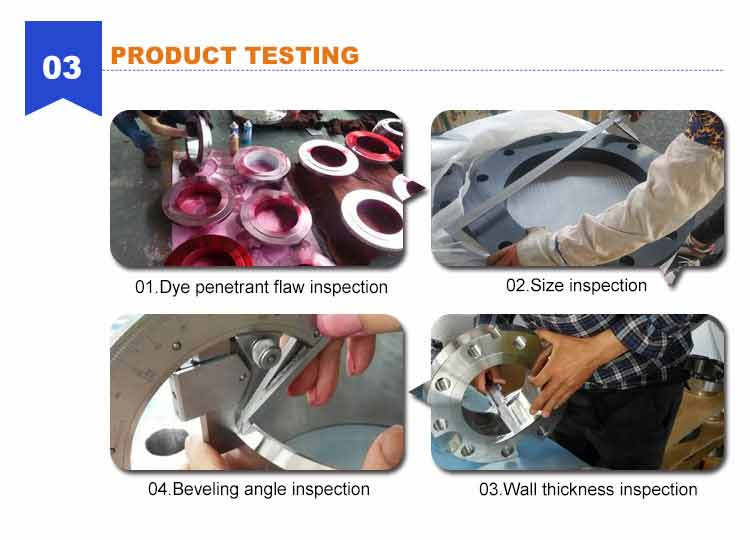
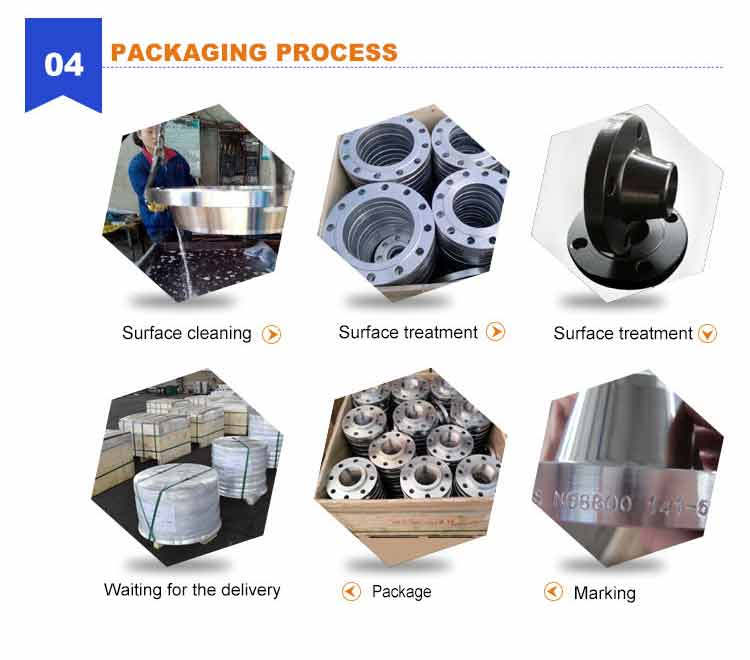
Blind Flange
Class 150 Blind Flange, Jis 10k Blind Flange, Blind Flange Price, Carbon Steel Blind Flange, En 1092-1 Blind Flange, Ansi b16.5 Blind Flange
HEBEI HANMAC MACHINE CO., LTD. , https://www.chinahanmac.com